About Us
Welcome to The Anne St. Clair Collection
For over 25 years, the heirloom-quality porcelain of The Anne St. Clair Collection has been cherished, collected, and gifted around the world.
The artist behind the collection is Anne Piazza and Anne’s family is steeped in the European heritage of the St Clair family. Anne began her artistic journey with a degree in classical art. Her studies later expanded to include Rosemaling (Scandinavian), Bauernmalerei (Bavarian), Chinoiserie (Oriental), and American folk art. With a rich heritage and diverse folk art training, Anne developed the unique technique and style that defines these timeless pieces.
Extensive global travel further enriched her artistic vision, adding cultural depth and sophistication to her designs. Anne’s goal has always been to create porcelain art of heirloom quality—pieces to be treasured and passed down for generations.
Her refined techniques and enduring designs come together to create the elegant works that have adorned trees and mantels in some of the world’s most storied locations.
One of the collection’s defining features is its repoussé effect—raised artwork created using a proprietary mixture of clay and glaze, known as slip. Once fired, the slip retains its dimensional form, resulting in the signature texture that blends old-world craftsmanship with modern artistry.
Rooted in Satsuma and American folk traditions, Anne’s work is a sophisticated fusion of classical and contemporary styles—detailed, distinctive, and truly exquisite.
Thank you for visiting our site and for your appreciation of our art.
The Anne St Clair Collection
About Our Production Process
Hand Crafted in the USA with Exquisite Attention to Detail
Each hand made ornament we produce is the result of a multi-step process that includes model and mold production, pouring, hand firing at extreme temperatures, multiple layers of artwork, and hand-signing and dating. See the details below and share our story when giving our ornaments as gifts to family, friends, and loved ones.
Step 2 - Mold Making
The model is then used to make a master mold. This is done the same way as it has been done for centuries. The bottom of the mold container is used as a platform and clay is built up to the exact centerline of the model. This is a slow process of working the clay into layers until the surface of the clay is perfect. The four walls of the container are then clamped together to form the shape of the mold.
This setup is used to produce a Master Mold which consists of one side of plaster with the model imbedded to the centerline.
This Master Mold is then used to produce production molds which must also be produced one side at a time.
Step 3 - Production Pouring
The production mold is used to recreate the shape of the model in porcelain. These molds are made of a special plaster which is hydrocephalic which enables it to absorb water. The proprietary clay made of a mixture of feldspar, flint, and kaolin, is mixed with water to the viscosity of motor oil and this mixture is called “slip”. The “slip is poured into the mold to fill it completely.
As the water in the clay slip is absorbed into the surface of the mold, it creates a very thin and delicate shell of wet clay. The slip is left in the mold for only a minute or less, and the excess is then poured out leaving a delicate, wet shell behind in the mold. The mold and shell are allowed to dry overnight. The next day the mold can be opened without damaging the unfired porcelain shell.
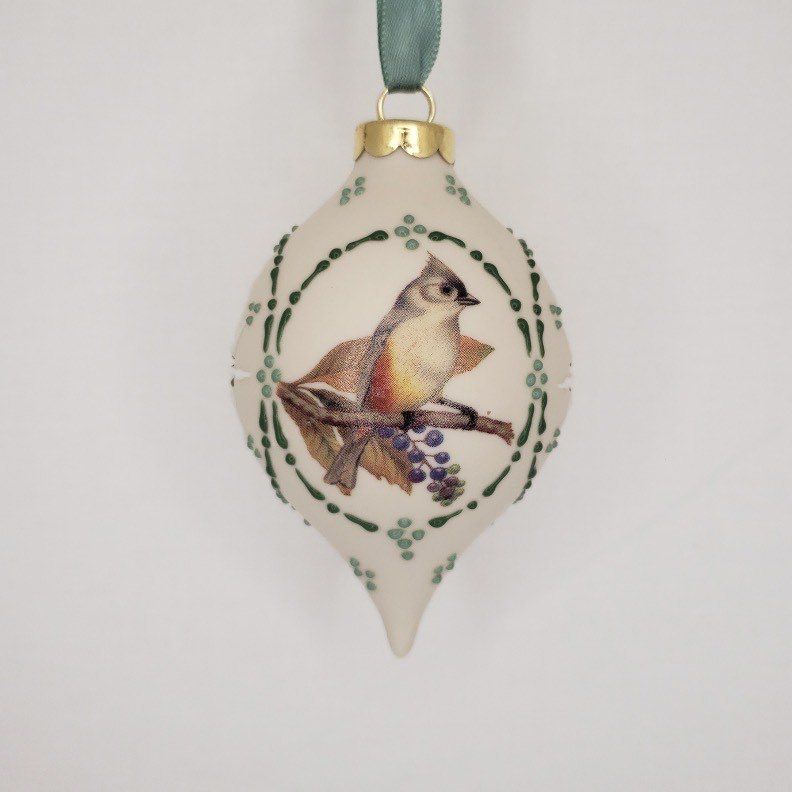
Step 4 - Firing & Cleaning
The porcelain shell is then placed into a kiln and “low” fired at 1267 degrees f. After an 8-hour firing and cooling period, the porcelain is partially fired to the point where it can be handled and cleaned without breaking.
During the cleaning process the seams, flashing and any, irregularities are trimmed and buffed off so that the surface of the ornament is perfect.
After cleaning the ornament, the blank is placed into another kiln and “high” fired to 2194 degrees f which takes approximately 12 hours, at which point it fully vitrifies and becomes a very hard bisque porcelain.
Next, the porcelain is taken to a special abrasive unit where the surface is carefully buffed to remove the course texture and make it smooth and semigloss to prepare it for the application of the art.
Step 5 - Artwork
Next, the ornament blank is graphed with a longitude and latitude line to keep the hand applied art concentric.
Next, the graphed blank goes to the artist who applies the first layer of art. The first layer could be stripes of glaze and/or the signature raised work known as slip trailing. This raised art is somewhat reminiscent of early Satsuma although much more intricate and complex. It has also been compared to the artwork on Wedgewood Jasperware although all our raised artwork is done by hand.
The ornament then is placed into another kiln and fired to a slightly lower temperature to vitrify the art while not damaging the blank.
After 12 more hours in the kiln the partially decorated blank receives another layer of hand applied art. This could be the first layer of a built-up clay motif such as a snowman or a Santa, or flat artwork composed of French Enamel that melts into the surface of the porcelain.
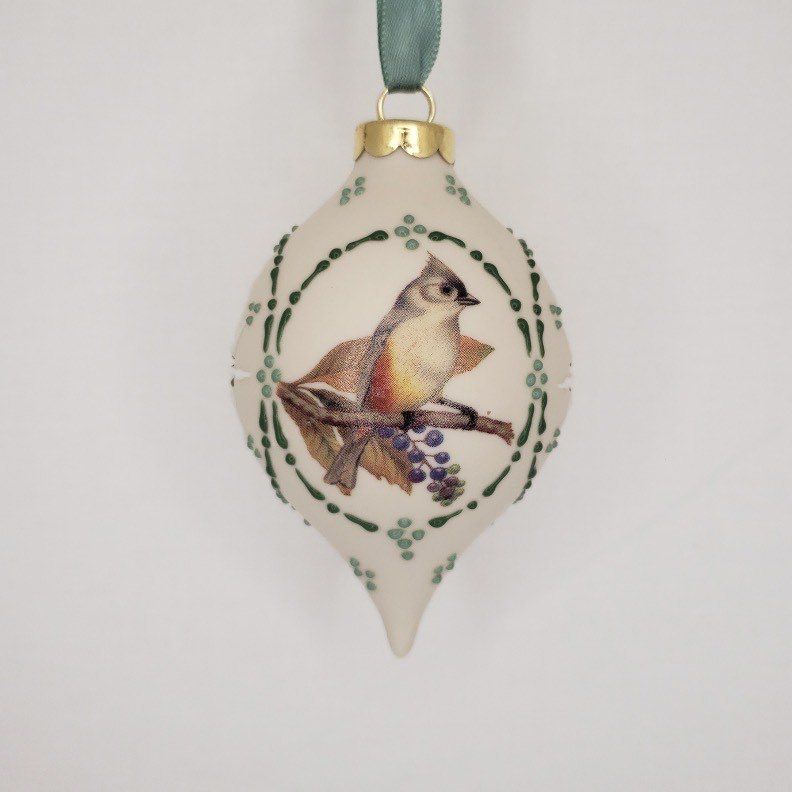
Step 6 - Gold Accents
Depending upon the particular artwork, a piece could go through one or two more firings to fire 22k gold accents or to complete the buildup of layered designs.